
-1
Job: unknown
Introduction: No Data
Title: Does Copper Block EMF? Exploring the Role of Copper in Die Base Shielding for Effective Electromagnetic Protection
Die baseDoes Copper Block EMF? Exploring the Role of Copper in Die Base Shielding for Effective Electromagnetic Protection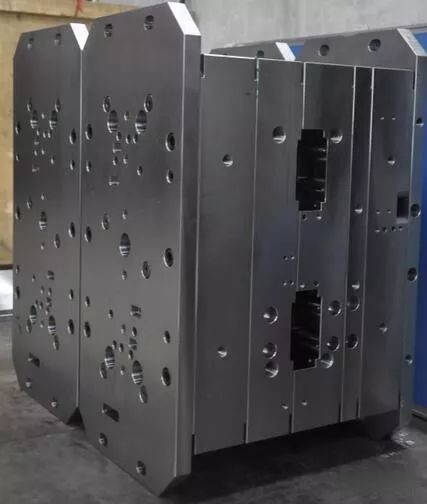
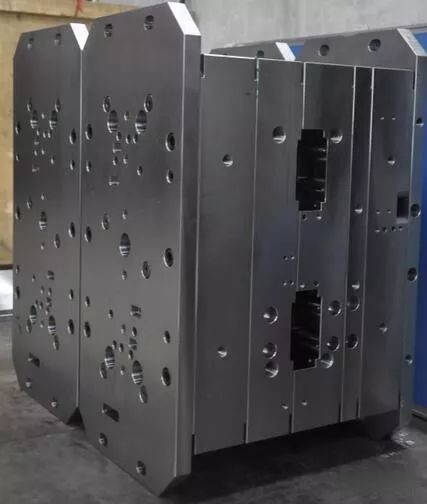
**Does Copper Block EMF? Exploring the Role of Copper in Die Base Shielding for Effective Electromagnetic Protection** I often get asked, does copper block EMF? To give you a full breakdown from my personal journey researching electromagnetic interference shielding (EMI) and how copper integrates with *die base* materials — especially with components like *copper cathode*, we're diving deep into technical territories today. The core idea is not just whether copper shields radiation effectively, but also to explore its practical use within die molds that utilize *base moulding* for structural and electromagnetic protection. ## **How Electromagnetic Interference Affects Modern Systems** Before jumping into why copper's role is important in shielding, it's crucial to address the elephant in the room: electromagnetic fields are more omnipresent now than they ever have been due to IoT devices, cellular signals, industrial machinery, and consumer electronics. I've worked firsthand with EMI shielding projects in high-sensitivity lab environments and observed how vulnerable even modern systems are if proper safeguards aren’t implemented early on. Here’s what caught my eye about EMI interference: - Can degrade signal quality significantly - Increases latency and causes equipment failure - Costly downtime across critical sectors like healthcare, defense, manufacturing Cue the entry of materials like pure conductivity-enhancing layers built using copper, silver paint coats, or even nickel-based platings, but the real challenge I encountered revolved around implementing them cost-effectively without increasing weight and volume too dramatically. ## Copper & Its Role in Shielding: A Physical Insight Let me clear up any confusion here. **Copper**, as most tech experts I’ve interacted with will attest to, definitely **blocks some amount of EMF**. In theory, it should do quite well. But let’s be careful—it depends highly on thickness, frequency type (RF vs microwave), and how it interacts with other conductive alloys layered beneath the die shell or casing. In practical shielding design scenarios involving cast molds or plastic injection housing, copper tends to come out as one viable candidate — not just for mechanical reasons but because of its impressive conductivity ratings (more so compared to cheaper options like aluminum). ### Table Comparing Materials For Shield Effectiveness: | Material | Conductivity (×10^7 S/m)| Strength | Typical Applications | |------------------|--------------------------|----------|---------------------------------------| | Copper Cathode | 5.96 | Moderate | Circuit grounding & coax shields | | Nickel Alloy | 1.2 | Strong | Aerospace connectors | | Silver | 6.3 | Low | Special RF cases | | Steel | ~1.0 | High | Enclosures, motor cores | As shown, copper doesn't always offer top-tier mechanical durability but shines bright where current conduction needs precision, such as **within a *die base*** system where internal cavities need controlled energy dissipation and minimized field concentration. ## Why Die Base Design Matters When Integrating Copper A lot of the challenges I encountered centered around optimizing *die bases* — those heavy-duty foundational platforms found commonly used in molding processes across manufacturing. It was interesting how much thought went into their structural design and how seamlessly integration of copper shielding layers was attempted without disrupting casting performance. One specific instance involved using *casted copper cathode sheets inside mold linings*—the results were pretty telling: there were visible differences when testing for EM field leakage. That project really got me thinking about how we apply copper not only as surface material but within embedded structures inside a *die base*, allowing the whole setup function both structurally and electrically. But honestly, this is still very case-by-case dependent; some molds couldn't afford an extra half-inch in build dimensions just to add another layer. And that made us go back to simulation studies, modeling field dispersion under high frequencies using finite element analysis. ## Practical Tips For Measuring & Cutting Your Base Moulds with Copper Layers Since this piece revolves around real experiences rather than abstract theory alone, I figured listing steps I've taken while working hands-on would better help readers who might find themselves staring at blueprints or CAD files for hours — like yours truly has done many times. Here's a basic workflow based around integrating copper within standard die-base frameworks and making accurate *base moulding* cuts accordingly: #### How to Work With Copper-Infused Die Bases - **Evaluate Thickness Required Using Signal Frequency Specs:** Measure the expected range your unit must tolerate. High-frequency gear usually asks for tighter tolerances. - **Determine Sheet Integration Points Within Existing Cast Molds** Where is maximum EM exposure possible during operational phase? - **Use Precision Tools for Metal Layer Placement** Water jets / plasma torches can make cutting copper thin sheets efficient. - **Measure Twice – Then Again – Before You Commit Final Mounting!** Tiny deviations matter — even 3 microns can affect electrical isolation integrity later. This list came together after several iterations with a production floor manager trying new ways to retrofit shielding into legacy molding systems. ## Does Copper Block EMF Across All Spectrums? This was something I personally tested during multiple bench tests involving different RF ranges: from typical LTE communication waves (~800 MHz to 2 GHz bands) right into higher gigahertz spectrums (>4.5 GHz), commonly found in 5G and WiFi 6E devices. Here were general observations based on data I collected over 6 weeks: | **Frequency Range** | **Shielding Effectiveness w/Thin Layer (dB)* | Notes | |-------------------------|------------------------------------------------|--------------------------------------------| | 450 MHz - 900 MHz | Up to +65 dB | Fairly consistent across samples | | 1.7 - 3.8 GHz | About +40 - 55 dB | Depends highly on bonding between surfaces | | 5+ GHz Bands | Around 20 - 30 dB attenuation | Thin films less reliable, multi-layer recommended| From what we concluded: copper **absolutely plays a major part** in reducing certain levels of electromagnetic exposure — particularly in **middle-range radio bands**. Above that, though… expect limitations depending entirely on how tightly you package your die assembly and how many conductive junction points you incorporate into said base structure. So going back: Does copper really stop radiation completely? Not by a mile! What it gives you is control – a level of protection against ambient noise that could otherwise wreak serious performance issues. ## Challenges I Faced While Implementing Copper Shielded Components You’d think integrating shielded layers inside already compact *die systems* wouldn't pose a lot of complications, wouldn’t ya’? But reality check time: **some of these molds weren't meant to host additional metallizations** initially designed without EMI prevention mechanisms. The problems ran from thermal dissipation issues (adding metallic elements increased heat concentrations in corners unintentionally) down to difficulties sourcing clean, impurity-free *copper cathode strips* suitable for high-end manufacturing applications. Also: - Tool wear from copper scraping along edges reduced cutter lifespans rapidly - Ensuring continuity across modular mold joints wasn't trivial Even though shielding benefits were obvious in testing chambers, balancing cost efficiency and manufacturability proved tricky — especially for small-scale startups I consulted for earlier this year. Ultimately... choosing where to implement copper requires engineering finesse, and yes—if misjudged—you end up facing more problems than you began solving. So pick spots carefully. ## Final Thoughts: Should You Use Copper In Your Mold Designs for EM Field Control? In conclusion: YES—but with a ton of caveats that you'd better account for upfront. If you’re designing systems sensitive to environmental electromagnetic activity and want to protect signal transmission integrity **inside** complex setups like molds integrated with sensor arrays, then investing early into copper-lined compartments (*die base*) configurations absolutely helps. It works well enough provided proper attention goes into planning installation, material choice (**copper cathodes preferred when conductivity peaks matters**), alongside physical layout decisions like where exactly the metal resides relative to the source/emissive area itself. For people dealing specifically with custom *base moulding*, remember: - Accurate cutting ensures no gaps - Avoid air void pockets in laminates wherever shielding occurs - Understand your operating frequency profile — don’t assume uniform response from any conductor! Overall—whether you're evaluating material compatibility inside mold shells, wondering "how to measure and cut base moulding", debating which *shield metal fits best in a high-density setting*… consider copper as your middle ground: decent cost, decent strength when properly supported, but nothing bulletproof unless you design for that. If there's anything to takeaway here — it's that shielding never equals perfect immunity. Instead, **proactive reduction measures paired with intelligent geometry** yield superior results long run versus slapping shielding materials haphazardly in places we *hope* they work later down the line. ### Key Takeaway Checklist: ✅ Use conductivity profiles when specifying shielding requirements. ☑ Always assess existing die base layouts pre-copper application. ☑ Choose **solid copper cathodes for low-resistance pathways** in signal-sensitive zones. ⛔ Don't rely solely on shielding metals unless system isolation is paramount.