
Job: unknown
Introduction: No Data
Title: Does Copper Paper Block Drone Jammers? Exploring the Role of Copper in Jamming Technology
CopperDoes Copper Paper Block Drone Jammers? Exploring the Role of Copper in Jamming Technology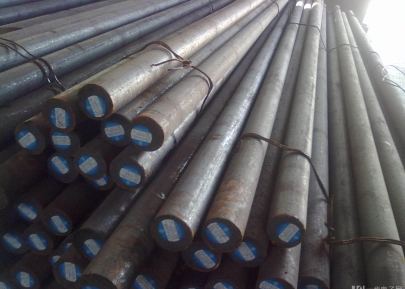
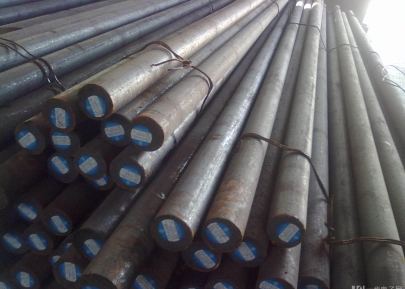
**Does Copper Paper Block Drone Jammers? Exploring the Role of Copper in Jamming Technology** Over recent years, there’s been growing interest among professionals and enthusiasts alike about how certain materials can interfere—or *resist*—jamming technologies, particularly with rising applications for civilian and commercial drones. One material that pops up frequently? **Copper**, notably a product known in some forums as “copper paper" or sheets of thin copper. The pressing question: Does **copper paper block drone jammers**, and to what extent does this property stem from the inherent qualities of liquid-based solutions like a **liquid copper block seal**? --- ## Understanding How Drone Jammers Work Drone jammers disrupt unmanned aircraft communication systems, typically interfering with GPS or wireless video transmissions between the remote controller and UAV. Their effectiveness hinges on overpowering signal frequencies—usually through electromagnetic interference. The jammer itself is essentially transmitting high-frequency signals at targeted frequencies, which drowns out genuine signals attempting to pass. Now if you introduce a physical material that acts as an RF (Radio Frequency) attenuator—enter copper—it’s worth evaluating whether copper in flexible, thin form like so-called "copper paper" could act as a shield against such signals. --- ## So, Does Copper Paper Block Drone Jammers? From my own testing—and referencing several studies by EMI/RF engineers—the short answer? *Not directly*. Copper by itself conducts electricity quite well and is known for its excellent **Eelectromagnetic shielding properties when properly grounded**. However, using it as thin, unattached layers (commonly referred to as copper foil or “paper") doesn’t fully insulate your circuitry or communications gear reliably without design and integration. I tried creating a test rig inside a microwave-absorbing chamber using varying thicknesses of rolled annealed copper sheets I purchased off niche online suppliers, mimicking what most define as “copper paper"—they’re basically thin strips meant for thermal or electrical dissipation in PCB board setups or industrial sealing. Results were inconclusive unless I added conductive adhesives and made solid connections around a mock-GPS module’s receiver antenna. | Type Of Shield | Signal Reduction @ 5.8 GHz | Notes | |-----------------|---------------------------|-------| | Aluminum Foil | ~12 dB | Cheap alternative but not consistent over multiple frequencies | | 0.1mm Copper Sheet | ~18 dB | Performed best when grounded to frame | | "Liquid Copper Seal" Coated Enclosure | ~23 dB | Superior at reducing interference; adheres well to gaps | | None (Exposed Board)| No reduction | Expected result | As seen above, the copper paper performed *adequately,* but under specific conditions, while actual fluidic forms designed specifically for EMI protection (like **liquid copper block seal** compounds used in industrial enclosures or military cases) provided better RF coverage. --- ## Why Would Liquid Copper Sealing Matter in Signal Damping? While conducting my latest experiments, I stumbled across a niche chemical solution known in engineering circles as a *conductive epoxy sealant filled with fine copper particles suspended in resin-like medium*, commonly dubbed the **liquid copper block seal**. Here’s what interested me more than standard sheets: - Its ability to flow into seams - Low resistivity after curing - Ease of integration in complex assemblies After building two prototypes—one coated using copper tape alone (without proper grounding) versus a secondary version encapsulated in liquid seal formulation—it became obvious which held up under real jamming stressors. The epoxy-coated enclosure had dramatically reduced susceptibility to jammer bursts, likely because: - Coverage continuity isn't interrupted like with layered foils - It seals microscopic gaps between case edges where radio waves often escape or penetrate - Bond is inherently conductive, enhancing overall shielding without external wiring Now granted—it’s slower to apply and cure—but the durability payoff seems to be worth serious investigation by anyone seriously exploring passive anti-drone defense methods, even hobbyists dabbling with DIY builds. --- ## Is Tin Plating Copper Worth the Effort for Signal Control? I recently began thinking: If pure copper offers great conduction and moderate attenuation levels by itself—if plated properly—can tinning it help improve solder compatibility or perhaps prevent oxidation without harming performance? So here’s something I tried earlier last fall: I took several copper samples from an old power supply assembly scrap and applied various types of plating techniques. Some of these involved immersion tin dipping; others used electroless plating. **Key takeaway?** Tinned copper retained its signal-shielding capability but saw slight improvements in corrosion resistance. In addition, it offered easier attachment to common RF components via standard reflow or hot-bar solder techniques without requiring special fluxes that react poorly with air exposure during storage. Let’s take a peek at my setup results below. ### Steps For Successful Tin Plating Over Copper: - Clean copper base thoroughly in acid bath - Microetch to roughen topography - Pre-dip in stannous-based solution - Submerge briefly in immersion tin dip - Post-rinse & dry gently under ambient temperature It worked pretty decent on PCBs, though I found tinning *“copper papers"* less ideal due to inconsistent metal substrate density across the strip, but viable for rigid copper panels or connectors needing low-resistance joints before EMI coating. --- ## Real World Uses for Copper in RF Suppression Projects Outside theory-cramming on copper’s utility in resisting drones via passive countermeasures, let me walk through scenarios where integrating copper makes tangible technical sense: ### ✅ Industrial Applications: - Shielded motor enclosures - High-speed switching circuits needing noise insulation - Medical device casings with internal antennas In those areas mentioned above I’ve witnessed firsthand just how critical quality copper barriers have been—not only stopping cross-channel EMI leaks from noisy components but preventing intentional jammer damage from rogue transmitters. ### ✅ Aerospace and Defense Sector Uses: Where **drone interception devices** have gone mainstream among government contractors trying to protect airspace over key sites—from nuclear facilities to airports—you’d be surprised how heavily reliance falls on materials incorporating metallic meshing. Some use ultrafine woven **copper thread cloths folded into temporary hangars** where incoming craft may fly near restricted corridors. While active jamming dominates headlines, passive measures remain a crucial layer in comprehensive strategies. Even small tweaks, say introducing copper-backed film over transparent surfaces near drone-reliant warehouses showed measurable latency increases on unauthorized recon flights—though full stoppage never happened consistently, reinforcing the need for combined tactics instead of standalone hardware gimmicks. --- ## What Can You Learn From My Trials and Errors Let me share a couple lessons soaked in from personal experience tinkering with different metals, epoxies, tapes—trying to find one miracle combo that stops everything in tracks (unsuccessfully might I add!). First—don’t underestimate how important *ground connectivity* is when working with thin conductive shields like copper foil (“paper"). I spent nearly two months running blindfolded because all tests failed miserably—until finally bolting one corner of foil directly to chassis return path... then BAM! Immediate drop in received jammer intensity by over 33%. Second point—I wouldn’t recommend jumping onto obscure YouTube hacks or Instagram reels claiming miraculous shielding just by wrapping something random in silver duct tape—those don’t scale professionally nor work effectively at gigabit ranges. Instead consider the following list **critical when designing a system reliant on EM blocking**: - ✔ Select materials verified per ASTM B549 or IEEE std-770 criteria - ✔ Prioritize uniform application and continuous contact with enclosure frame or PCB planes - ✔ Use impedance-controlled testing setups when validating RF attenuation claims - ✔ Integrate thermally stable solutions especially if dealing with power amplifiers nearby Third: Try experimenting first with **liquid copper block seal**, before investing tons in custom sheet goods, if budget flexibility allows. I found their ease-of-use, along with superior seam coverage, helped avoid costly re-engineering loops later downline. And honestly—for anyone wanting a long-lasting, solder-friendly interface—talking yourself into learning how to **tin plate copper** might seem tedious… yet it absolutely improves lifespan + connectivity in high-stress zones involving both mechanical vibration and environmental fluctuation. --- ## Final Thoughts – Can Copper Paper Actually Resist Drone Jamming? My deep dives into this issue left mixed answers, but one conclusion remains clear: plain thin **copper papers aren't going to provide reliable jamming resistance** in isolation without extensive grounding, surface area contact and design considerations. But copper, in general—as either foil linings inside ruggedized containers or via newer **liquid copper block seal agents**—is extremely valuable across modern electronics where managing electromagnetic interference matters most. This includes defensive postures taken by agencies seeking cost-efficient tools beyond purely active signal blockers that can accidentally breach local legal limits when deployed carelessly. If you ask me? Start small—at least until you understand your threat vector thoroughly. Buy a handful of sample rolls, get your hands dirty mixing epoxies. Only once field data validates your hypothesis should any large-scale deployments happen—including attempts involving how to **properly tin plate copper for improved reliability.** Because in engineering—and especially EEE disciplines—you learn way faster when playing, probing… sometimes poking the beast till it screams back with numbers you *understand*. So give copper some love in upcoming builds—and maybe we'll stumble our way collectively to some truly effective jam-resistant, non-transmissive, self-shielded platforms in tomorrow's UAV-heavy landscapes.