Optimize Your Mold Base with Copper Blocker: A Complete Guide for Industrial Efficiency
Hello again, fellow industrial pros. Over the past several yeers of working hands on with mold bases and all sorts of molding tools—I'm sure you knoe what I'm talking about—you realize just how small changes in components can seriously effect efficiency across the whole run. Today, let's dive into a specific yet under-talked solution that's quietly been boosting production floors from good to really reliable—the humble but mighty copper blocker.
Understanding Mold Base Components
You might be wondering where exactly this "mold base" fits into our overall process.
- Support structure: The mainframe where all mold components are anchored;
- Precision mounting: Every component like bushings or cavities is aligned to the mold’s core and cavity inserts;
- Simplified replacement: Having your tool setup standardized makes troubleshooting easy when something needs adjustment (especially important during mass runs).
For context, here is a quick table highlighting basic sections of any traditional base molding assembly:
Component | Purpose | Criticality Level |
---|---|---|
Ejector Plate | To assist ejection mechanism | Medium |
Locating Ring | Mates machine nozzle with sprue bushing | V.High |
Copper Blocker (Key Focus Area) | Aids in reducing heat buildup at critical points | High |
What Makes a Copper Blocker Unique?
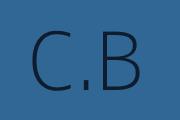
In short terms a copper blocker is a specialized piece often added in certain mold base configurations to prevent overheating or localized thermal stress points caused by long-term friction. Unlike generic inserts used mainly as alignment pieces, copper blockers serve more as a functional component aimed at prolonging lifespan of both internal mold surfaces and ejected plastics over repeated use.
-
// check if CSS applies
- ✔ Acts as a cooling barrier against mold wear
- ✔ Prevents unwanted sticking around gate areas
- ✔ Low maintenance once installed correctly
How To Select the Right Grade & Design
When considering a purchase of copper blocker set—specifically the copper knife block set variety—make sure you ask yourself: What types of polymers does my line work with regularly? If dealing predominantly in softer materials (think PPs or polyethylenes,) a medium-density grade may suffice without excessive investment per unit, however for highly heat sensitive resin types (like polycarbonate) a full alloy blend copper blocker with nickel coating will give better long term return. Here's a short checklist before ordering new sets:Efectividad Térmica (%) | Promedio costo (USD/piece) | Uso recomendado | |
---|---|---|---|
KC22 |
|
$13.5 | Termoplásticos rígidos y cargadas |
DJX340 | ★93 | ~$17 each | Polímeros técnicos y compuestos complejos |
GFX82 (Niquel coated) HIGH RECOMMENDED FOR BASE MOLDING | >94 | $21 USD approx. | Cualesquiera resina sensible al calor + largas jornadas sin parar producción. |
*Note: Performance values are based off field tests between '23-'24 from multiple factories using varied setups (results could vary +/-2%)
Built For Efficiency – Where You See It Pay Off
Let's talk shop for a second—if your current base molding layout doesn’t have these blockers built-in, it’s possible to modify after manufacturing (with some precision), but honestly? If budget allows integration at original stage saves us a few man-hours plus potential damage downline. Here's how they directly help: - Heat Dissipation Control: With molds often reaching temp above 260°F repeatedly—heat tends accumulate around pinholes and eject areas unless managed via cooling passages OR via insertion blocks made from thermally conductive material like high-conductivity copper.In practical terms: 7 to 9 seconds reduction on average cool cycle due to lower mold temps maintained during operation phase—doesn't look much but multiply that across thousands of pieces being pressed every hour...
**Other secondary boonefits observed during testing periods** included: * Less frequent oil application near gates, * Improved surface finish consistency especially along thinner regions like flange edges. * Reduced burr occurrences in post-processing steps.
Trouble Spot Elimination Tips When Upgrading
While copper may conduct well and resist some degree of pressure... we shouldn't overlook minor issues related to expansion mismatch with steel mold frames. Tip No.1 - Use slight clearance gaps in housing holes where applicable, say 0.03 - 0.07 mm depending size so the metal expansion upon temperature increase has room to breathe without applying lateral stress. Tip no. 2 – Always champer contact edges even slightly to allow better flow through coolant pathing and reduce chance build up. TIP NO.3 – IF INTEGRATED ALONG SIDE A "CU KNOCKER BLOCK" UNIT, VERIFY ALIGNMENT MATCH BETWEEN SEATING AREAS PRIOR INSTALLATION.Criticas Consideration Checklist Pre-installatn (My Personal Notes!)
Make sue this list isn't missed when prepping your team:- Copper Quality Certification - Make sure alloys comply to either UNS C11000 standards or similar. Some cheaper versions mix too mch zink or phosphrous which kills performance long term.
- Steel vs copper thermal expantion coefficient compatibility – best practice uses aluminum-sprayed mating parts when combining in same frame
- *BONUS ALERT: Try running your copper inserts first at partial capacity (about 70% max design output). Monitor results, then go live if acceptable yield holds