Read the full article in HTML format.
The Role of Copper Alloys in Mold Steel Applications: Enhancing Performance and Durability
Copper alloys might seem out of place when you’re dealing with tough mold steel applications — especially if you’ve primarily worked with standard mold steel grades like P20 or H13. Let me tell you firsthand, having been in industrial tooling for almost fifteen years: ignoring the benefits of copper’s thermal conductivity is akin to running a high-performance car with regular engine oil — possible, but not ideal.
In my early days in die casting manufacturing, one of my colleagues insisted on using copper-backed **heat blocks** in specific molds where thermal management was critical due to inconsistent part quality and longer cycle times. At first glance, integrating materials like brass or beryllium-copper felt like complicating an already complex system. But after seeing the performance boost from that initial test, it changed our approach altogether. Today I’m sharing what we’ve come to know about how copper contributes to enhancing durability, speed, and efficiency — particularly when paired with common mold materials like **carbon steel plates** and traditional steel setups.
---The Thermal Edge Copper Offers in Die Casting Tooling
From personal experience on the shop floor, copper-based inserts (specifically beryllium and chromium-zirconium variants) act as excellent heat conductors inside mold tools where rapid heating and cooling occur. The issue? Conventional mold steels — even good ones like H13 or NAK80 — tend to trap heat. Over time, this trapped heat can create hot spots that result in warpage, uneven surface finish, and accelerated mold fatigue.
*Sample view inside a mold showing strategic copper insert locations.*
Here’s a little chart from data we gathered over three months testing two identical mold setups—one with and one without copper integration:
Criterium Measured | No Copper Insert | Copper Heat Block Applied |
---|---|---|
Mold Cycle Time per Part (in sec) | 145s | 129s (-11%) |
Surface Temperature Differential (∆F) | +45°F variation | ±5°F |
Premium Tool Steel Longevity (est.) | 70K cycles | ~100K–105K cycles |
That level of control matters — and it translates to real productivity on the floor without unnecessary downtime caused by premature degradation or maintenance checks that pop up too often on older systems.
- Dramatically reduced temperature variation across the mold cavity
- Lowers localized expansion stress points under continuous use
- Improved dimensional stability and lower scrap yield during mass runnings
Why Carbon Steels Need a Boost in Critical Spots
I’ve spent most of my life shaping and machining molds using mild, pre-hardened **carbon steel plate** structures. Sure, these are economical for base mold structures — no doubt about it. But they don’t hold up thermally under prolonged exposure to extreme cycling temperatures.
“Adding copper heat sinks isn't just another engineering fad—it’s based in physics and material dynamics."
In areas near gates or runner sections — where molten materials make contact for prolonged seconds each shot — adding a beryllium-copper block makes absolute sense. It dissipates excessive energy away faster than low-grade chrome-alloyed steels or typical SAE steels like 1018, which were once the standard in many foundries back in the mid-90s until more advanced options became affordable.
---Types of Molds Best Suited for Copper Alloys
I’ll be the first to say not every mold application requires extensive alloy modifications with high-end materials — however, in certain niche applications, copper becomes absolutely indispensable:
- Zamak & Mg Pressure Dies: Where fast cooling improves metal integrity and minimizes sink mark retention.
- In-Mold Injection Cavity Tools for polymers: Copper-backed inserts improve ejection timing predictability due to uniform shrinkage behavior across plastic resins under stable temps.
- Cores prone to “thermal ratchet," like deep cavities in aluminum casting — here, **Copper inserts** manage peak load fluctuations much better than any ceramic coating attempt could.
So, unless the application doesn’t involve sustained thermal activity, there really shouldn't be an excuse not to explore these possibilities in your mold construction process, assuming production demands justify the cost differential — more on that below.
Metal Type | Thermal Conductivity (BTU/hr·ft·°F) |
Tensile Strength (ksi minimum avg.) |
Machining Rating Relative |
---|---|---|---|
H13 Tool Steel | 14.3 | 211+ | Easier than 17-4 stainless |
BeCu Alloy C17200 | 157+ | ~82 to 97ksi* | *Harder to drill and mill |
Limitations You Might Not Have Considered
A big concern early on was cost vs value proposition — because copper tends to wear quickly during long operations compared to harder steels. And unlike a carbon plate used in non-core structural regions, you must protect it from abrasive contact if your parts have particulate-heavy additives or operate beyond recommended hardness levels (~HRC 30 maximum seems safest for extended insert use).
Machining Complexity: One lesson we had to learn the hard way: Beryllium copper, while incredibly strong when precipitation-aged, dulls carbide tools twice as quickly versus machining mild steel. So expect a spike in tool replacement frequency. In smaller shops lacking multi-tool automation lines, this is worth careful budget planning for labor costs before adopting new processes with higher-integration materials.
---The Cost Debate Isn’t As Clear Cut As Many Claim
- Beryllium-copper is expensive — yes
- Savings come through longer uptime between reworks
- Efficient production reduces part defect ratio dramatically – sometimes improving OEE by 8% or more depending upon machine rate and volume
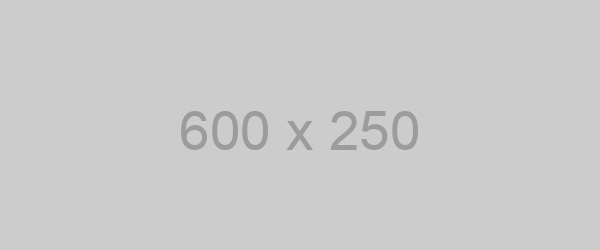
Estimated ROI over two-year period comparing hybrid setup using Be-Cu components versus all carbon structure in selected toolsets.
The graph isn't exact because each facility has variations (material thickness, part design variance etc.) – but it demonstrates why some facilities keep coming around, especially as lead-time pressures intensify due to fluctuating OEM needs and supply chain challenges from post-2020 onward.
This kind of predictive decision making, informed through past mistakes and small tests done cautiously with sample builds, gives manufacturers a lot to think about. I still see engineers who hesitate at upfront investments, yet they struggle with unexpected downtime weeks or months down line. My own journey reflects a pattern that's fairly universal among those involved in modern tooling practices.
---Conclusion — Is Copper Necessary Or Just Nice?
If you ask me today whether to include a copper heat block when building a complex or highly demanding set-up: I say do it selectively — not everywhere, but exactly where the mold's weakest thermal bottleneck resides.
Main Points Recap:
- Thermal efficiency gains from using copper are real and repeatable with right mold designs;
- Properly installed Cu-alloy segments reduce mold failure risks by lowering hotspots dramatically;
- Cost implications are offset within few thousand shots if volumes justify the upgrade
- Degradation is mostly manageable through protective shielding or periodic plating
While it may feel counterintuitive mixing soft, traditionally nonstructural metals into heavy duty dies — experience has shown otherwise. Especially in tight-margin scenarios and ultra-competitive production runs where fractions of seconds mean differences in profit, thermal performance plays its role quietly but critically.
As industries push forward towards smart moldmaking environments and adaptive machinery stacks driven by AI analytics, we cannot ignore the fundamentals built directly beneath these evolving surfaces: materials science, metallurgy, and precision engineering — all things I’ve dealt with firsthand and continue advocating to younger designers trying navigate an increasingly complex world of production requirements.