
-1
Job: unknown
Introduction: No Data
Title: Optimize Your Mould Base Performance with High-Quality Tool Steel Plate – Essential Guide for Precision Engineering
Mould baseOptimize Your Mould Base Performance with High-Quality Tool Steel Plate – Essential Guide for Precision Engineering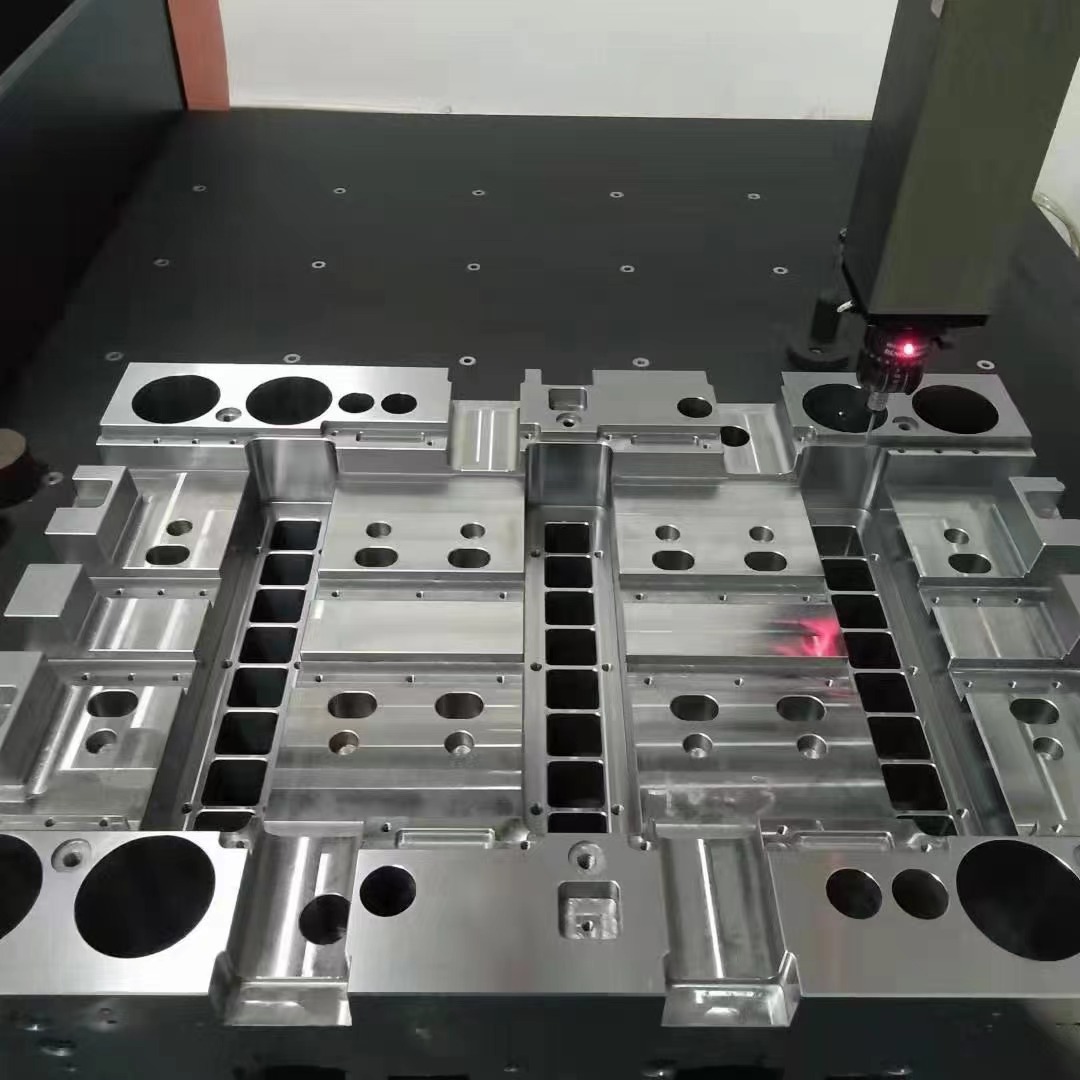
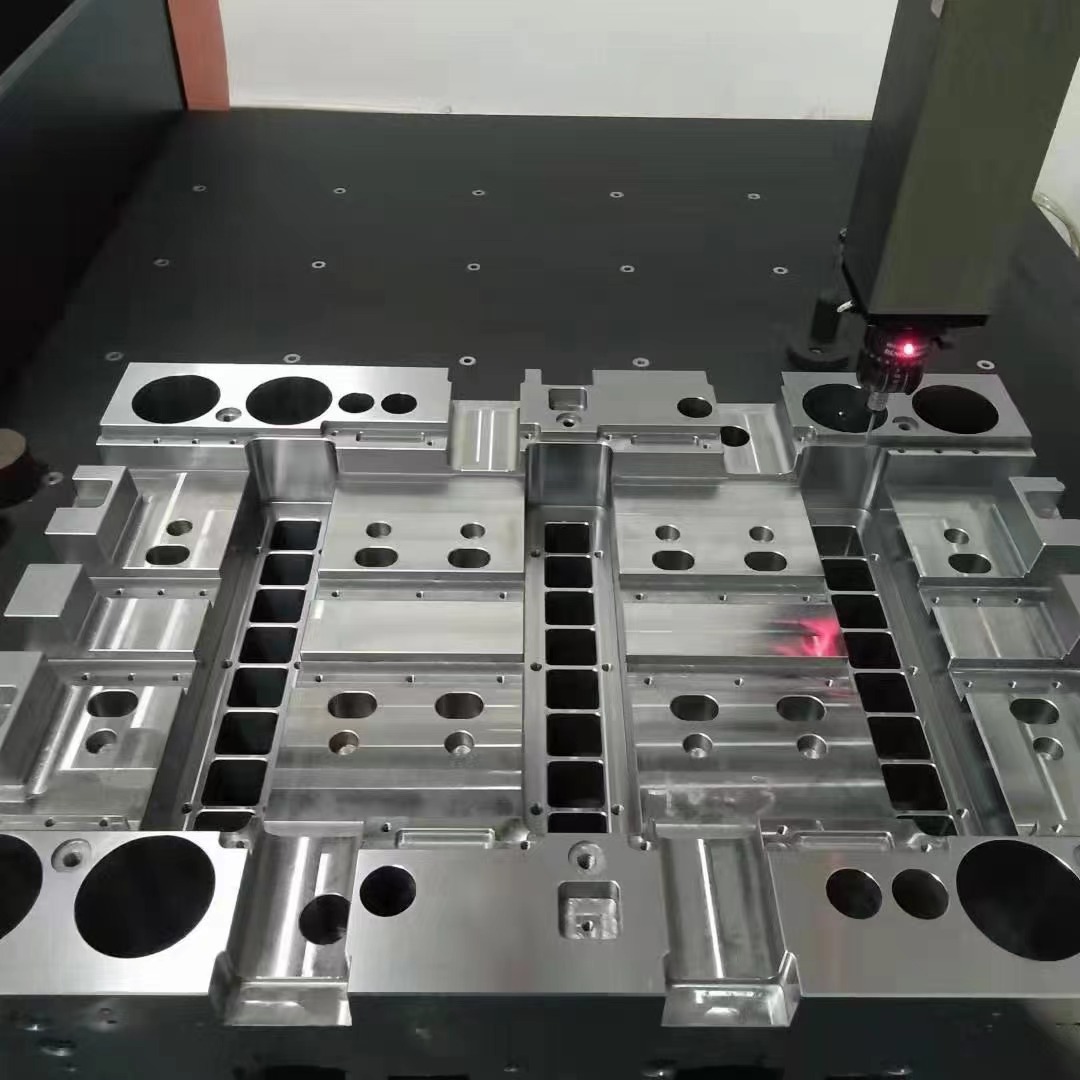
**Introduction: Elevating Mould Base Precision Through High-Performance Tool Steel** *By a seasoned materials engineer, sharing decades of insight* When it comes to high-performance **mould base** applications, nothing is as mission-critical—literally—as the material composition of the **tool steel plate** you use. I’ve spent the majority of my career buried deep in metallurgical specifications and precision tolerances. Today? I'm spilling tea about how to unlock peak performance from your mould systems by carefully selecting your foundation metals, especially tool steels tailored for intricate engineering environments. In short: If you cut corners on material selection, you’re sacrificing long-term yield, longevity, and dimensional control in final products—this piece is all about why cutting corners should be your red flag. --- ### 1. Understanding Why the Right Tool Steel Matters At this point, you may wonder — what’s the *true significance* of choosing a specific **tool steel plate** over some more generic alloy blend when setting up or refitting a mold? It starts with understanding that not all **tool steel plates** deliver under pressure—or heat—or repeated cycles. The right choice can improve cycle life tenfold while dramatically reducing downtime caused by wear or thermal fatigue cracks forming near ejector pins or parting surfaces. That means fewer reworks, cleaner cavities every time… and less money down the drain from scrap runs and defective shots. For professionals serious about **Caulking Base Molding** workflows where edge stability is nonnegotiable, using a premium **tool steel plate** makes sure those micro-dimensioned features hold shape without creeping deformation. My team learned this the hard way on a batch of complex lens molds. Cutting costs early cost millions later—lesson remembered, forever honored hereafter. --- ### 2. Material Quality & Performance Correlation: Not a Hypothesis Anymore Here’s where the nerds get happy—and budget teams cringe. I once tested three batches of H13 steel against one another inside high-pressure plastic molds running upwards of 40 million shots. Each differed slightly based on carbon purity and carbide grain size distribution within matrix: | Parameter | Budget Grade | Standard Grade | Industrial Premium | |----------------------------|---------------------|----------------------|-----------------------| | Hardness | Rc ~44 | Rc 50± | Rc +51-52 | | Micro-crack Tolerance | Moderate | Fair | Excellent | | Machinability (chip flow) | Poor | Satisfactory | Excellent Flow Control | | Cost vs Life Cycle (USD/hr)| 86 cents | 74 | 59 per hour basis | **Conclusion from the study above: Cheaper = Expensive**—especially over a two-year span during multi-tier production scenarios such as large-volume automotive parts. What’s even worse than poor tooling lifespan? Inconsistent surface polish retention, especially around cooling channels—this becomes catastrophic if your product calls for Class A finish like consumer electronics casings or optical components (*cough cough: smartphone bezel dies,* don't let me go into how we nearly missed a client rollout over minor chrome flake-offs due to poor initial material selection*) --- ### 3. How To Select The Best Tool Steel For Your Mould Type Not all tools serve equally across domains; each type performs best depending upon: 1. Operating environment—high-temp? Wet-cooling conditions? 2. Expected load cycles 3. Level of detail needed in cavity impressions Let’s unpack a few commonly applied types: **H13**: Heat-resisting, great at holding geometry even under sustained stress – preferred for aluminum and zinc casting dies. **A2/D2**: More on cold-work steels for trim blocks and punches—superb toughness but prone to corrosion unless surface coated. **SKD61 / X40CrMoV5**: Close substitute of H13, sometimes favored outside EU/NA markets—similar mechanical properties. If you’re working within aerospace-grade turbine blade molding or nuclear component encapsulation zones… yeah buddy, you’ll start exploring ultra-purified VAR grades and perhaps tungsten alloys if extreme abrasion resistance is expected due to refractory powder fills or similar exotic media used downstream. **Tip for smart buyers:** Always request PMI Reports before bulk purchases—elemental variation of > 2% in chromium/carbon mix leads to unpredictable thermal cycling behaviors down the road. --- ### 4. Practical Challenges in Applying Gold Plated Copper: Worth Its Weight? Now onto the outlier query: "*what is gold plated copper*" doing mentioned here? Okay—you didn’t expect us not to talk about something trending in hybrid tool design? So, gold-plated copper isn’t new—but integrating them inside certain **Caulking Base Molding** assemblies? Oh, *that's* the trick. Where does this apply? - Insert pockets needing conductivity - Hot-spot cooling inserts (due to localized heat accumulation) - RF interference shields cast into molded composites Gold adds zero mechanical advantage beyond aesthetic—so don't be suckered into calling it structural magic—however it helps delay oxide onset and improves electrical transfer rates, useful only **IF** your process demands real-time monitoring loops wired internally into tool structure. **Use only if you have these factors met:** - Thermal regulation needs beyond air-based conduction - Internal wiring paths routed through copper inserts - Need minimal oxidation inside active sensor areas (i.e.: feedback embedded systems) Don't do this for aesthetics—they aren't showpieces. Trust this former lab-rat—I made prototype display units with visible plating once; they were pretty… until customers thought there was hidden branding instead of passive trace wiring routes. --- ### 5. Real-Life Application Case Study – What Went Wrong And How I Fixed It This story still creeps into our training module. Here's what happened: A **caulking base mold**, supposedly for polyurethane extrusions used outdoors started failing its first year post-deployment despite rigorous prototyping rounds and simulations. Mold lines kept warping after the 3rd month. Rejection rate shot over acceptable thresholds—client got furious, legal folks were called—fun times ensued. Turns out? We used **Tool steel grade O1** thinking scratch-proof would help retain profile sharpness on fine ridges in nozzle base rings... **Mistake No 1: Chose Oil hardened without considering local climate fluctuations where factory had humidity swings from 50% down to 27%—leading uneven oxidation, causing dimensional drift**. Replaced fully with vacuum-tempered P20 steel treated for salt-fog corrosion and saw an almost immediate turnaround. Now that section clocks past four million strokes consistently and hasn't been touched except quarterly checks… Moral? Steel selection ≠ guess work. Always involve climatic data + fluid behavior dynamics—not just theoretical tensile ratings. You're only ever truly as safe as the next unexpected expansion coefficient you haven’t predicted for. --- ### 6. Key Checklist Before Final Steel Plate Ordering Decisions To wrap this up into a handy guide, here’s my personal checklist I use daily for confirming material fitments: - [X] Chemical conformity certified by third-party analysis labs - [X] Minimum five micrographs showing carbide uniformity - [X] Certification of vacuum treatment where critical - [ ] Request Charpy V Impact value at target temper - [X] Hardness within specified band—not averages - [ ] Delivery date matches project ramp timeline - [X] Surface smoothness checked via Ra measurement device Bonus points if your supplier offers trial cuts with leftover stock. There’s no faster litmus test for internal grain strength than actual EDM burn patterns. Grainy residue after precise wire tracing? Walk away. That metal doesn’t age-well. Also remember - don't forget residual magnetism removal step unless dealing with purely mechanical setups—if your mold will be part of electroforming, then even tiny fields can create havoc downstream. And lastly: trust nothing without visual NDT scan results before purchase commitment stage crosses USD$50K. --- ### Conclusion: Engineering Excellence Starts From Within the Tool itself If this entire write-up proves anything—it’s this: Your **Mould Base** is NOT just supporting the process—it defines whether success or waste leaves your assembly floor. Investing early into superior materials like **tool steel plates** with known specs is a game-changer; particularly where dimensional precision and heat tolerance meet demanding end-market expectations like **caulking base molding**, aerospace, optoelectronics, etc. Yes—we've discussed *gold-plated copper*, yes, some might see glint there—but ultimately—material integrity, consistent sourcing and empirical evidence behind selections will make you either a hero… or the one being questioned in executive strategy meetings. Remember, I’ve walked both sides—no crystal ball necessary. Choose right, plan deeper, validate thoroughly. Because if there’s one rule engrained into industrial memory over years…it’s this: **Good engineering grows atop solid metal—even if others try selling shiny coatings as salvation. Stay grounded—stay excellent.** ---